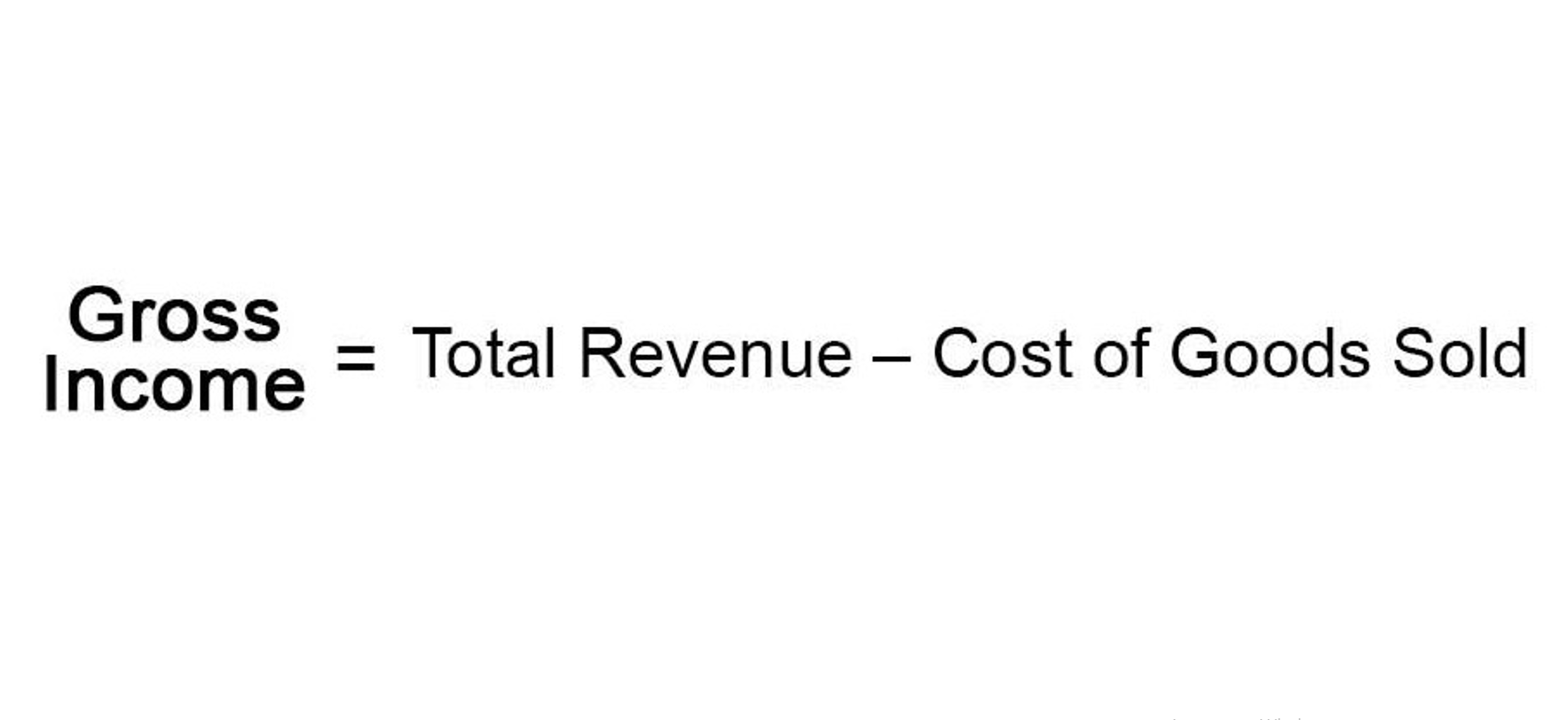
Per Generally Accepted Accounting Principles , such inventory is generally written off as a production a financial loss to the company. A contra account “provision for obsolete inventory” is used to write down the inventory. Expense is debited in the income statement and credited in the provision for obsolete inventory account.
- The burden of file maintenance can be an obstacle in using advanced inventory calculations to keep inventory at the correct levels.
- With more than 1,000 member organizations worldwide, APQC provides the information, data, and insights organizations need to support decision-making and develop internal skills.
- If you really want to free up space and get rid of a lot of inventory at once, group items together for one price and offer the bundle at a reasonable rate.
- Whatever your options to reduce inventory levels, the first step is to identify which items are potentially in excess and at risk of becoming problematic, whether raw materials or finished goods.
- This could be anything from time-based branding , to holiday-themed candy, snacks or beverages.
Along with inventory management, having visibility over your inventory at all times is key. With today’s technology and customers’ high expectations, the product lifecycle has become shorter across industries, making inventory become obsolete much faster (e.g., fast fashion). Since you cannot sell obsolete inventory, it is considered a loss and can cut into profit margins. A write-down occurs if the market value of the inventory falls below the cost reported on the financial statements.
Storeroom managers know that carrying costs such as taxes, infrastructure, and insurance can be as high as 16%-25%. The other reason, and this may cause you more visible problems, is the lack of storage space in your storeroom. Excess and obsolete inventory for manufacturers can be 15-20% of stock. Warehouses often expect 15% of products to be returned, rejected or become obsolete. The total cost of this inventory can be as high as 25% when considering the cost of the storage, shrinkage, damage and the time value of money. My company has excess/obsolete inventory that was purchased ~5+ years ago.
How To Avoid & Reduce Obsolete Inventory
For instance, refrigerant that was purchased as a qualified product but is no longer allowed due to EPA regulations is dead inventory. It serves no purpose and takes up space for refrigerant bottles that are compliant and can be used. Inaccurate or incorrect forecasting of customer demand can cause you to order more stock than you need – leaving you with obsolete inventory after selling only a portion of what you stocked. Inventory that has reached the end of its useful life and isn’t expected to be sold is known as obsolete inventory.
Read on to discover the bad practices you might have engaged in that contributed to your obsolete stock. Hearst Newspapers participates in various affiliate marketing programs, which means we may get paid commissions on editorially chosen products purchased through our links to retailer sites. Inventory reserves evaluation to identify and review all inventory to proper estimations on a quarterly basis. Put simply; the term refers to items that are either impossible or very difficult to sell. Here are few tips on avoiding outdated inventories if you have lost your excessive stock and want to make sure that you never deal with it again. If you are trying to transfer your warehouse as much stock as fast as possible, you can also bundle goods and deliver a discount on a bundle. There are companies that would purchase the goods at the lowest possible price in order to free up storage space and cash.
Method 2method 2 Of 3:getting Rid Of The Inventory Download Article
Social media sellingis a great way to gauge what marketing messages are working and what aren’t. Gary’s organization, the National Association for the Exchange of Industrial Resources , can help you get a tax break for donating your obsolete inventory. The result was that Microsoft had a massive store of unsold Zunes that they had to simply write-off as a loss. Obsolete inventory is a warning sign that you haven’t been following inventory management best practices.
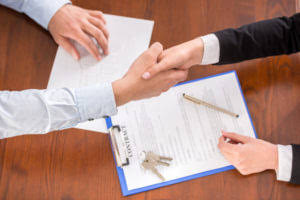
Improving your sold cost recovery rate can be challenging, but it ultimately is one of the key influencers of a liquidation program’s financial performance. Essentially, it’s the amount of excess inventory that’s actually sold, as compared to the amount that was available.
You could even bundle items AND offer a discount on the bundle if you’re trying to move as much stock out of your warehouse as quickly as possible. If items aren’t selling individually, bundle them with items that are similar or sometimes bought together. Obsolete inventory write-offs are a common practice for reducing excess stock.
Sell At A Discount
Life Cycle Institute’s approach to high impact learning integrates learning, leadership and change management competencies to produce documented, sustainable results. Most ERP systems allow you to run an ABC listing of inventory items. Force yourself to look at the C’s and D’s on the bottom of the list at least once a quarter and take action. Sales knows which customers represent real risk, build that information into your ordering decision process. The technical storage or access that is used exclusively for anonymous statistical purposes. If you don’t, you’ll inevitably order more than you need or order products your customers don’t want.
Cost of goods sold is defined as the direct costs attributable to the production of the goods sold in a company. Depreciation is an accounting method of allocating the cost of a tangible asset over its useful life to account for declines in value over time. An inventory write-off is an accounting term for the formal recognition of a portion of a company’s inventory that no longer has value. APQC (American Productivity & Quality Center) is the world’s foremost authority in benchmarking, best practices, process and performance improvement, and knowledge management . With more than 1,000 member organizations worldwide, APQC provides the information, data, and insights organizations need to support decision-making and develop internal skills.
Taxes
You do a review of your inventory and determine there is $10,000 worth of obsolete inventory. A write-down is needed if the market value of your inventory part falls below the cost that has been reported in your records. As such, this type of inventory must be written off or written down, which can result in a large loss for your parts department. Be sure to look at a range of results, not just one liquidation event, to make sure you’re accurately seeing the average performance and not basing your benchmarks on an outlier.
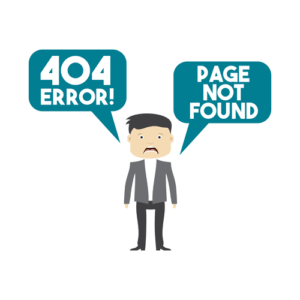
Innovations that make the products worthless, inconvenient, unattractive, etc. Kristina is the Director of Marketing Communications at ShipBob, where she writes various articles, case studies, and other resources to help ecommerce brands grow their business. To learn more about how ShipBob can help you optimize your supply chain, click the button below to start the conversation.
A business first has to figure out if the inventory has any value. For example, if a grocery store has milk become obsolete via spoilage, it has to be disposed of and thrown out. In that case, the accounting method would subtract the disposal value from the book value, take that amount as a debit on inventory and credit inventory write-off. The word “obsolete inventory” refers to inventory that has reached the end of its product cycle. This inventory has not been sold or used in a long time and is not likely to be used in the near future. Such inventories must be recorded and may cause a business to suffer significant losses. Obsolete inventory is also known as excess inventory or dead inventory.
How Inventory Adjustments Affect Income Statements
A write-off involves completely taking the inventory off the books when it is identified to have no value and, thus, cannot be sold. Obsolescence is an especially difficult problem for modern automotive parts departments due to the speed of technological improvements. As a result, the life cycle of parts is becoming shorter, increasing obsolescence at a much faster rate. We’ve seen a lot of variation in sell through rate in the industry, but it’s typically one of the biggest opportunities for improvement. One major manufacturer saw a 33% increase in sell through rate after starting to manage it through Spoiler Alert.
- An inventory write-off is an accounting term for the formal recognition of a portion of a company’s inventory that no longer has value.
- Material Requirements Planning Production planning, capacity planning, raw material purchase scheduling.
- Regardless, don’t expect to get anywhere near what the initial investment was when the items were purchased.
- Check out EAL Green as one example that has been used by manufacturers.
- Similarly, inventory can become obsolete due to some disaster such as being damaged by fire etc.
These are all challenges that every retailer and e-tailer needs to navigate and work with, especially given the volatile nature of the global supply chain presently. One means of dealing with the inevitable shipping delays is to manage a safety stock that can serve as a buffer when capacity runs scarce. However, a risk arises from carrying too much inventory for too long; it becomes obsolete.
Finally, if inventory write-offs and outside warehousing are continuous problems, you may want to consider assigning the disposition and prevention responsibility to a specific person. We have done this with several clients and the pay-off is always good. It is rarely a job anyone wants long term, so they have the incentive to work on the issue aggressively. The last time this level of change occurred was in 1986, which was under President Ronald Reagan. The new tax reform bill could bring around change for manufacturers, and in a very positive way making life…
If you have a surplus of inventory that isn’t going to sell, then donate it to charity and get some tax deductions. If you have obsolete inventory, the best thing to do is deal with it right away. If you have too much inventory on hand that’s not selling, chances are you want to know how to get rid of it. If you’ve identified slow-moving inventory, the first step is to notify your team that there’s a concern with that inventory item. That way no one will accidentally order more or fail to take action on a sales plan. Perhaps a buyer scanned the wrong SKU for an order and you ended up with cases of the wrong item. Or, perhaps your supplier didn’t tell you how long the lead times would be, causing you to miss the profitability window on your purchase.
- Most businesses determine that its inventory is obsolete once there are no sales after a set amount of time.
- Regardless of where you’re at today, it’s essential to establish a clear baseline so that you can measure future progress.
- A write-down occurs if the market value of the inventory falls below the cost reported on the financial statements.
- The result was that Microsoft had a massive store of unsold Zunes that they had to simply write-off as a loss.
- The company will try its best to minimize the inventory obsolete cost as it is the cost that does not provide any benefit to the customers or company.
- Many companies will set internal protocols for managing slow-moving inventory.
- You can sell them at a discount, bundle them with other products, liquidate them through surplus resellers, try to remarket them to a different audience, or do a complete inventory write off.
We previously defined excess inventory with a very simple explanation. Basically, excess inventory is any inventory that exceeds projected demand, and is therefore not expected to sell. There can be many causes, and inventory becoming obsolete is one of them. It’s important to know exactly what we’re talking about when we say excess inventory and obsolete inventory.
It’s easy to accumulate too much stock if you automatically re-order without checking your inventory numbers. Turn off the automatic re-ordering and see how quickly the products are selling before you decide to replenish them. For example, a product might be obsolete if it’s costing you more money to store and promote than you’re making in sales. Auctions are a great way to dispose of a lot of inventory in a short amount of time, but it will cost you to set up the auction and staff the event.
Retrieve Items To Remarket
If a manufacturer is sitting on excess product on December 20th, how should they qualify that inventory? Chances are it was slow-moving up until that point, and in five days it’s going to be obsolete, unless the product has enough shelf life for it to make it to next Christmas . In this case, if a manufacturer keeps holding onto it, its customer guarantee date will come and go, thus pushing it into true short-dated territory. Similarly, when a company rebrands a product or makes a design change, many retailers are hesitant to sell the previous packaging, rendering it obsolete. This is common as manufacturers move toward eco-friendly packaging and experiment with different packaging sizes. Packaging changes can be great for sales — Coca-Cola saw a 10% boost when they introduced the Fridge Pack in 2002 — but can also leave a lot of obsolete inventory.
This option is more applicable to people with finished goods inventory. It is far less likely to be an option for a manufacturer carrying parts inventory. Check out EAL Green as one example that has been used by manufacturers. The Distributor Board provides Advisory Board and Consultative services to wholesale distribution companies. The Distributor Principles have owned, run, managed, https://www.bookstime.com/ and advised successful distribution companies for many years. Areas of particular specialization include Strategic Planning, Mergers & Acquisitions, Technology, Operations and Sourcing.Visit or e-mail The technical storage or access is required to create user profiles to send advertising, or to track the user on a website or across several websites for similar marketing purposes.